以下是五金冲压件设计时需要注意的几个关键参数说明
五金冲压件设计的关键参数
五金冲压件设计是连接产品功能与制造可行性的环节。为确保零件质量、生产效率和成本效益,必须重点关注以下关键参数:
1.材料选择与特性:
材料类型:根据零件功能(强度、硬度、导电性、耐腐蚀性等)选择合适的金属材料(如低碳钢、不锈钢、铝合金、铜合金等)。
材料厚度(t):直接影响零件的强度、刚度和冲压工艺难度(如小弯曲半径、拉深深度)。设计需明确标注公差。
材料性能:材料的延伸率、抗拉强度、屈服强度、硬度、n值(应变硬化指数)、r值(塑性应变比)等至关重要,它们决定了材料的成型ji限(起皱、开裂风险)、回弹大小和终强度。
2.冲压工艺性与结构设计:
小弯曲半径(Rmin):避免弯曲处开裂的关键。通常要求内弯曲半径R≥(0.6-1.0)*t(具体取决于材料和状态)。过小的R会导致材料外侧过度减薄甚至开裂。
孔/槽间距与边距:孔与孔之间、孔与边缘之间需保持足够距离(一般≥t,复杂情况需更大),防止冲裁时变形、塌角或模具强度不足。
脱模斜度:对于拉伸、成型件,侧壁需设计适当斜度(0.5°-3°),确保顺利脱模,减少划伤和磨损。
圆角设计:避免尖锐的内外角。内圆角半径(Ri)建议≥0.5t,外圆角半径(Ro)建议≥t。足够大的圆角能改善材料流动、减少应力集中、防止开裂、延长模具寿命。
拉深比/减薄率:对于深拉深件,需严格控制每次拉深的变形程度(直径比、高度比、减薄率),防止起皱或拉裂。
3.尺寸与公差:
功能性公差:根据零件在装配和使用中的要求设定合理且可实现的尺寸公差、形位公差(平面度、垂直度、位置度等)。过严的公差会大幅增加模具成本和调试难度。
冲压工艺公差:理解冲压(尤其是弯曲、拉伸)带来的固有偏差(如回弹、扭曲),在设计阶段进行补偿或预留调整空间。明确关键尺寸基准。
4.模具可行性考量:
冲裁间隙:凸模与凹模之间的间隙(通常单边取材料厚度的5%-15%)直接影响断面质量、毛刺大小、模具寿命和冲裁力。设计需明确材料厚度和类型。
材料流向与搭边:排样设计需考虑材料纤维方向(影响弯曲性能)和必要的搭边值(保证条料刚度和送料稳定性),直接影响材料利用率。
模具强度与寿命:零件结构应避免过于细长的凸起、悬臂或薄弱区域,这些易导致模具局部应力集中、磨损快甚至崩刃。考虑废料是否易于排出。
总结:成功的冲压件设计是材料科学、结构力学、制造工艺和成本控制的综合体现。设计师必须深入理解这些关键参数之间的相互影响,在满足功能需求的前提下,追求工艺的稳健性、率和低成本。与模具工程师、冲压工艺师的早期沟通至关重要。
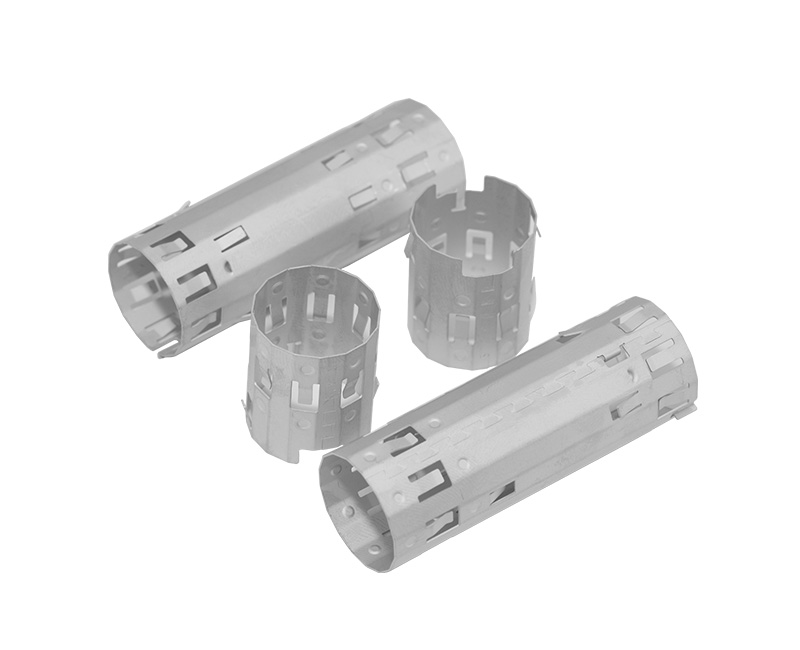
上一条:如何提高五金冲压件的使用寿命?
下一条:没有了