多工位五金冲压件成型技术对比分析
多工位五金冲压技术通过工序集成实现生产,主要包括级进模冲压、传递模冲压、多工位压力机冲压及机器人自动化冲压四种典型工艺,其技术特性对比如下:
1. 级进模冲压技术
通过模具内连续排列多个工位实现全自动加工,材料经开卷机连续送料,单次冲程可完成冲孔、折弯、成型等多道工序。优势在于生产效率极高(可达800次/分钟),适合微型连接器、端子等大批量小型零件。但模具开发成本高(约50-200万元),调试周期长达3-6个月,且对材料利用率敏感(通常65-85%)。
2. 传递模冲压技术
采用独立机械手在工位间传递坯料,每个工位单独设置模具。相比级进模,更适用于汽车结构件等中大型复杂零件(如车门铰链),可处理厚度达6mm的板材,成型精度±0.05mm。设备投资约300-800万元,生产节拍15-40次/分钟,适合年产量50-200万件的中批量生产。
3. 多工位压力机技术
集成式压力机配备转塔式工位系统,通过伺服驱动实现模具快速切换。优势在于柔性化生产,切换产品仅需2-4小时,适合家电面板等中小批量订单。机型采用液压+机械混合驱动,吨位可达2500T,能耗降低30%,但维护成本较高(年均约设备价值的8%)。
4. 机器人自动化单元
由工业机器人(常用六轴)联线多台单工位压机,特别适合新能源汽车电池壳体等深拉伸件。采用3D视觉定位系统后,定位精度可达±0.1mm,投资回收期约2-3年。但受限于机器人负载(通常≤200kg),适合单件重量<15kg的中型零件。
技术选型建议:级进模适用于微型件大批量生产;传递模侧重复杂结构件中批量;多工位压力机适合柔性化需求;机器人单元则针对特殊工艺或人机协作场景。企业需综合考量零件尺寸(<50mm优选级进模)、年产量(>500万件推荐级进模)及产品变更频率进行选择。
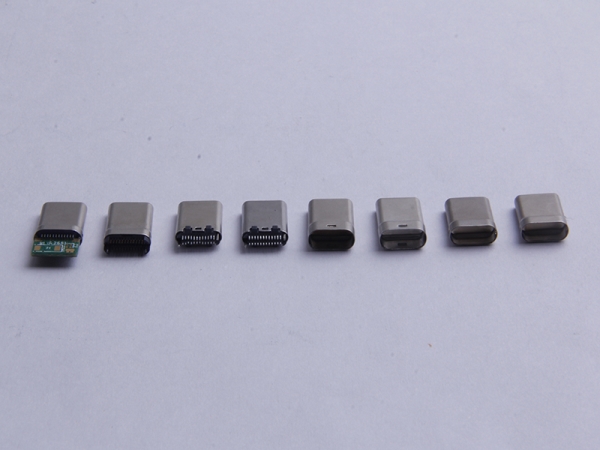
上一条:五金冲压件AI视觉检测应用案例
下一条:5G通讯设备屏蔽罩冲压工艺