精密连续模冲压件加工流程解析
精密连续模冲压是一种、高精度的金属成型工艺,广泛应用于电子、汽车、家电等领域的小型复杂零件制造。其在于通过多工位模具设计,在连续送料过程中完成冲裁、折弯、拉伸等多道工序,实现“一模成形”。典型加工流程如下:
1. 原材料准备
选用高精度金属卷材(如铜合金、不锈钢等),通过开卷机展开并矫平,确保材料表面无划痕、氧化层,厚度公差控制在±0.01mm以内。
2. 模具设计与调试
连续模采用级进式结构,包含冲裁、成型、分离等多个工位。需通过CAE优化排样方案,确保材料利用率>85%,并设计导向系统(如滚珠导柱)和快速换模机构。模具间隙需按材料厚度5%-8%调整。
3. 自动化冲压
使用高速精密冲床(300-1200SPM)配合送料机,以0.01mm级精度完成连续加工。典型流程:
- 工位冲导正孔定位
- 中间工位完成冲孔、折弯、拉伸
- 末工位切断分离成品
关键参数需实时监控,如冲压力(50-300吨)、行程速度等。
4. 后处理与检测
零件经退火消除应力后,进行电镀/喷涂等表面处理。采用三坐标测量机(精度±1.5μm)检测关键尺寸,光学投影仪检查轮廓度,并执行盐雾测试验证耐腐蚀性。
5. 质量控制要点
- 模具定期维护(每5万冲次研磨刃口)
- 在线视觉检测系统监控毛刺(≤0.03mm)
- 动态平衡调试避免材料扭曲
该工艺相比单工序模效率提升5-8倍,尺寸精度可达IT7级,适合大批量微型精密件生产。实际应用中需重点关注模具寿命管理及材料回弹补偿设计。
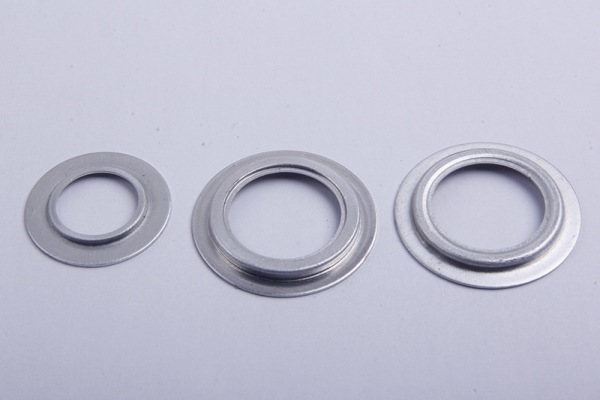
上一条:五金冲压件批量生产成本核算方法
下一条:微型五金冲压件激光去毛刺技术