车用铝合金冲压件模具寿命提升关键技术分析
随着新能源汽车轻量化发展,铝合金冲压件应用占比持续提升,但模具寿命不足成为制约生产效率的痛点。本文从材料、工艺、设计三个维度探讨模具寿命提升路径。
1. 材料优化:模具基材与表面处理协同升级
针对铝合金粘模性强、热膨胀系数高的特性,优先选用高硬度、抗粘附模具钢(如SKD11、DC53),并通过TD处理(碳化钒涂层)将表面硬度提升至HV3000以上,降低铝材转移风险。同时,采用多重复合涂层技术(如CrN+TiAlN复合PVD涂层),在保证涂层附着力的前提下实现耐磨性与耐高温性(600℃)的协同提升。
2. 工艺参数智能调控
建立冲压速度-温度耦合控制模型,通过有限元确定铝合金佳成型区间(通常控制在200-250℃,速度0.3-0.6m/s)。引入红外测温与伺服压力实时反馈系统,动态调节模具预热温度(建议120-180℃)和冲压节拍,避免因温度波动导致的应力集中。
3. 结构设计创新
(1)优化模具间隙设计,将单边间隙控制在板厚的10%-12%,配合R角抛光至Ra0.2μm以下
(2)开发模块化镶块结构,对易损部位(如拉延筋、切边刃口)采用可拆卸设计,局部更换成本降低60%
(3)增加辅助导向机构,将模具对中精度提升至±0.02mm,减少偏载磨损
4. 全生命周期维护体系
建立模具健康档案,利用3D扫描检测关键部位尺寸变化,当圆角半径磨损超过0.15mm或涂层剥落面积达5%时启动修复程序。采用纳米复合润滑剂(含二硫化钼+石墨烯成分),使摩擦系数降低至0.08以下。
通过上述技术集成应用,某主机厂B柱加强件模具寿命从8万冲次提升至22万冲次,单件模具成本下降37%。建议企业建立"材料-工艺-检测"闭环优化机制,结合数字化手段实现模具寿命的管控。
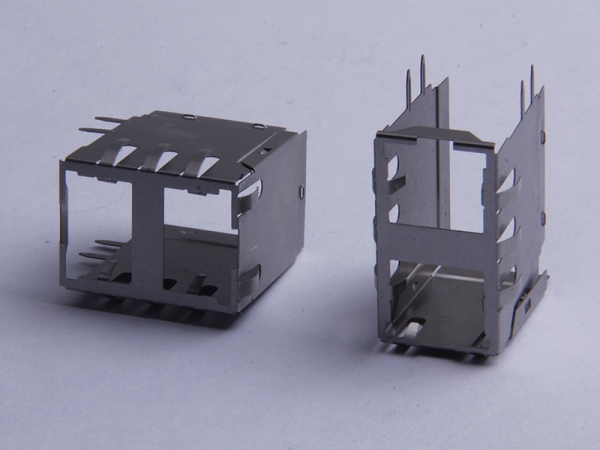
上一条:五金冲压件一站式ODM服务流程